P20 Mold Steel
P20 Mold Steel is a versatile, low-alloy tool steel that is characterized by good toughness at moderate strength levels. The steel is commonly used for plastic injection mold cavities and tooling and for die casting dies for zinc. P20 is typically sold in the pre-hardened condition at a hardness of approximately 300 HBW.
Composition
C | Mn | Si | Cr | Mo |
0.33 | 0.80 | 0.65 | 1.75 | 0.40 |
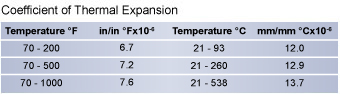
Physical Properties
- Density: 0.284 lb/in3 (7861 kg/m3)
- Specific Gravity: 7.86
- Modulus of Elasticity: 30 x 106 psi (207 GPa)
- Thermal Conductivity:
24 Btu/ft/hr/°F
41.5 W/m/°K - Machinability: 60-65% of a 1% carbon steel
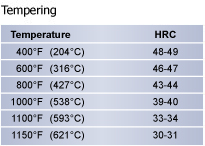
Heat Treating Instructions
Stress Relieving
Preheating: Because P20 is sold in a pre-hardened condition, hardening heat treatment is not necessary. After machining and intermittently during service, the steel must be thermally stress relieved by heating to 900ºF (482ºC), equalizing and holding for one hour per inch (25.4mm) of thickness, and cooling in air to ambient temperature.
In those rare circumstances where the steel must be re-hardened, the steel must first be annealed prior to hardening.
Hardening
Critical Temperature:
Ac1: 1405ºF (763ºC)
Preheating: Heat at a rate not exceeding 400ºF per hour (222ºC per hour) to 1150-1250ºF (621-677ºC) and equalize.
Austenitizing (High Heat): Heat rapidly from the preheat to 1550ºF (843°C). Soak for 30 minutes for first inch (25.4mm) of thickness, plus 15 minutes for each additional inch (25.4mm).
Quenching: Pressurized gas, or interrupted oil to 150-125ºF (66-51ºC).
For oil, quench until black, at about 900°F (482°C), then cool in still air to 150-125°F (66-51°C).
Tempering: Temper immediately after quenching or cryogenic treatment. Hold at the temperature for 1 hour per inch (25.4mm) of thickness, 2 hours minimum, then air cool to ambient temperature. Tempering temperatures and hardness are given in chart above.
Annealing
Heat at a rate not exceeding 400°F per hour (222°C per hour) to 1450°F (788°C), and hold at temperature for 1 hour per inch (25.4mm) of maximum thickness; 2 hours minimum. Then cool slowly with the furnace at a rate not exceeding 50ºF per hour (28ºC per hour) to 1150ºF (621ºC). Continue cooling to ambient temperature in the furnace or in air.